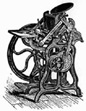 |
How
Paper is Made
Click here for the Paper Making Virtual Tour!
The
basic raw material for the papermaking process is wood. To begin the
process, pulpwood logs must be reduced to chip form. Prior to chipping,
logs are passed through a debarking drum (large, open-ended cylinder).
Within the drum, logs collide with one another and rub together removing
the bark. The bark falls through slots in the cylinder walls and is
collected and burned as fuel in the power boilers. The debarked logs are
conveyed to a chipper, which reduces them to small 1.5- to 2-inch
squares with a 0.25-inch thickness.
Softwood and hardwood chips are kept separate until the pulp is blended
at the paper machine since each has its own physical properties. Wood is
made up of small cellulose fibers, bound together by a glue-like
substance called lignin. In the pulping process, these fibers are
separated by cooking the wood with chemicals to dissolve the lignin.
To accomplish this, the chips are loaded into large vessels called
digesters on either a batch or continuous basis. Digesters are designed
on the same principle as a kitchen pressure cooker. The chips and
chemicals are steamed under pressure for 1.5 to 4 hours until the
mixture is reduced to a wet, oatmeal-like mass. The cooking frees the
fibers so they can be suspended in water.
The pulp is blown from the digesters under pressure to separate the
fibers. It is then washed to remove the cooking chemicals and dissolved
lignin and then bleached to the proper shade of whiteness. From there,
the pulp is passed through refiners. These refiners roughen the surface
of the individual pulp fibers by loosening the threadlike elements from
the fiber wall so they cling together when formed into a sheet. Added
after refining are dyes and other additives to give the finished paper
the desired properties.
Water is then added to the pulp in a ratio of 200 parts water to one
part fiber. This furnish, as it is called, is then run onto the forming
fabric or wire of the paper machine. The forming fabric is an endless
mesh screen that circulates at the wet end of the paper machine. There
the fibers become interlaced, forming a mat of paper, and much of the
water is extracted.
Traveling at speeds of more than 3,000 feet per minute, the paper is
pressed between water-absorbing fabrics and wound through a series of
steam-heated cylinders called dryers, where the last of the water in the
sheet is removed. At this point, the paper passes through a size press
that applies a starch solution to both sides of the sheet. Sizing seals
the surface so ink cannot soak into the paper during printing. Since
sizing wets the paper, the paper must again be dried by traveling
through another series of steam-heated drums.
After drying, the paper goes through a calendering process that provides
a smooth finish by ironing the sheet between heavy, polished rollers. At
the dry end, the paper is wound onto spools to form a machine reel and
then rewound and slit into smaller rolls on a winder. Some of these
rolls are sent for sheeting and packing into cartons. Others are rewound
to smaller-sized rolls and wrapped for shipment.
A
screen is used to separate larger chips
(From: http://www.internationalpaper.com/Our%20Company/Learning%20Center/How%20Paper%20Is%20Made.html |
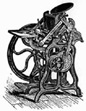 |